Now that the joists and the plywood support for the concrete floor are in place, it is time to layout the interior partitions and prep for the concrete pour. The interior partitions are simply marked on the plywood with a marker, this is because the radiant heat tubing is not installed under a partition - which would simply waste heat and potentially risk puncturing the tubing when the partitions are fastened down.
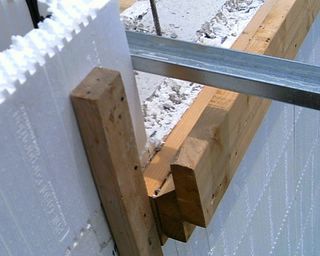
The wood is the form for the edge of the porch. The outer ICF panel is used to hold in the concrete for the floor. However, since the inner panel is not in place, there are no webs to give the wall any rigidity. The steel stud is used for that purpose, and also to help hold the forms straight.

This is the holding tank that we had installed for the future basement bathroom. We are having this roughed in right now, as it will be much more expensive (and disruptive too) to have this done later.
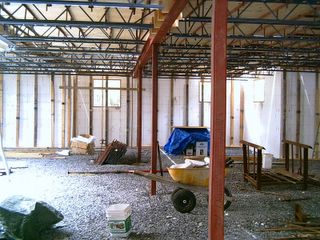
This is a view of the basement. You can see the steel joists with the roll bars holding up the plywood. The finished height in the basement - under the joists - will be almost 8' (7'11').

This is the view of the underside of the porch - or the cold storage room, in other words. There are two doors from the basement to the cold storage area. Freda and I both really like squash and are hoping to be able to buy them at harvest time and then keep them in here to enjoy throughout the winter.
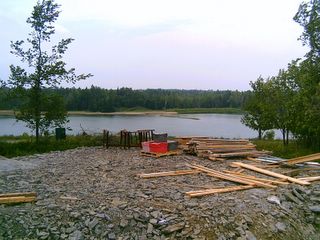
If you turned around when you are facing the future front door, this is the view you would see from the porch. Isn't this a beautiful sight!?!