This is a house blog once again. It is also an occasional dog blog, flower blog, and bird or other creatures blog...
Sunday, October 30, 2005
Day 206 - Warehousing... (updated)
We have been picking up things here and there over the past four months or so, when they have been on sale. So far, we have:
- laundry room floor (Armstrong commercial vinyl tile)
- laundry room sink and faucet
- main bath sink faucet and bath/shower faucet
- lights for master suite closets
- exterior light fixtures
- master bedroom light fixture/fan
- powder room faucet (although just discovered this is wrong)
- glass door for master bath (will be mounted as a pocket door)
- exterior door hardware - levers and locks
- house numbers and door bells
- microwave/range hood combination
- laundry room light fixtures
I may have forgotten a few other things too.
We have ordered and put a deposit down on:
- interior doors (Masonite Palazzo, plus french doors for foyer and solarium)
- fireplace
- plumbing
All of these guys required that we read over every line of the purchase order and sign it before taking a deposit. I am not looking forward to the next Visa statement!!
We have selected, but have not ordered or put a deposit down for these items:
- flooring
- light fixtures
- cabinetry
- trim styles
- light fixtures
- garage doors.
We are working on:
- propane supplier (we got a good tip from Kim Miller, one of Mark's former colleagues)
- electrical plan
- fence
- finding a way to fix the powder room faucet problem
- paint colours (to be honest, Freda is doing the heavy lifting on this really)
Still to do:
- select stucco colour, texture, and supplier (need to get samples from Charles)
- select aluminum fascia/trim colour
Fence
Freda has been researching some companies that install chain link fence. We want to have a fenced area so we can let Tawny run loose in the back yard. Ostensibly this would also be to contain any visiting dogs, but Freda is concerned about keeping the local bears, coyotes, wolves, and porcupines away from Tawny. (I am not concerned about the bears (they would stay away), and think Tawny could take care of herself, if pressed, by a coyote or wolf although we would not want that to happen of course. Porcupines are another story, we've already had that $500 vet experience, thank you very much!!)
However, most fencing companies won't work past mid- to late-November and it is quite unlikely that (a) the rock in the area we would like to have fenced in will magically disappear by then, and (b) the septic lines need to be installed before the
And for some really great news...
We took lunch out to the crew on Saturday. When we were leaving we bumped into Steve Berry who told us that he found three sites for the excess rock on our property, so we won't have to spend a penny to get all that rock shifted. Fabulous! And the best part is.... this should all happen before the snow flies! Absolutely wonderful. Thank you Steve!
Saturday, October 29, 2005
Day 205 - Some VSPs!!!
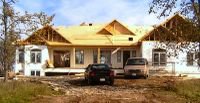
Both false dormers are installed. The peak is not completed, and also the roof over the 2nd bedroom (not visible here because it is at the rear of house on left). The Chris-mobile and Dave-van are parked here because the driveway was churned up by digging the hydro trench, so is quite uneven.

The septic field area was prepared. You can see the Canadian Shield (rock) poking out in a few places here. Because of all the rain we've had over the last 4 weeks, the dirt was quite mucky today.

The trench was dug and the conduit (sans cable) was installed. After it is inspected, the cable can be run, but the panel can't be powered up until the roof is on. Apparently some silly rule because water and electricity don't play well together! :^))))
Wednesday, October 26, 2005
Day 202 - A very pleasant surprise!

The roof is coming along. A false dormer is now in place.
"Neither rain, nor sleet, nor snow, nor gloom of night shall keep the postman from his appointed rounds."
That's what Freda and I thought about the crew when we found out that they had been working this week in the steady rain. Because of all the rain lately, we had expected to see little progress when we went out to the land. And most of the crew are also going to work on Saturday if the weather is good (it is forecast) to make up a bit for all the rain last week. What a pleasant surprise! We are glad we have such a dedicated team!

Bell Canada delivered the underground telephone cable so we popped out to the site to drop it off. I took these photos when we were out there.
We plunked down a deposit on the fireplace today - a 42" clean view from Kingsman Industries, who manufacture them in Winnipeg, MB.
Charles, Dave White, and Steve Berry marked out the septic field on Monday, with Steve Berry. Steve is going to move some of the excess material around for us.
Charles came over this evening to clarify something Dave said. Afterwards, we talked about what's coming up next...
Roof - complete truss installation and sheathing. Three trusses are missing so the roof may be complete except for that.
Hydro - Dave White will come on Friday and dig the hydro trench and place the conduit for the hydro, cable, and telephone cables. That will be inspected next week, and (once the roof is on) then the hydro service can be installed. After that...
Driveway - build up driveway and do some grading around the house with some of the excess material there in piles. Put a wheelbarrow load or two (haha!) of Granular A (crushed rock that passes through a 3/4" sieve) on the driveway. That will make it usable for cars, as the bumpy nature of it is really only useful for trucks. Charles actually got a flat on his truck because the rock punctured the tire.
Garage floor - Install drain in the garage floor, and install mesh, heating tubing, and pour concrete (maybe in two weeks).
Stone - Conrad has ordered the stone from Merkley Supply so he will get started on that when the stone comes in.
Stucco - waiting for quotes from the stucco installers. We need to select colours still.
Garage Doors - we have selected the installer, but need to wait until the floors are poured before he will install the doors.
Roof shingling - will be a go as soon as the roof is sheathed and it is not raining.
Once the roof is on and the windows in, we will be calling the bank for an appraisal and a draw on the mortgage, and sign the papers at the lawyers. Also, a bunch of the other trades can start coming in and doing their thing. We will be glad when all that starts to happen.
Tuesday, October 25, 2005
Plumbing fixtures ordered

From a budget perspective, we are slightly under budget for the plumbing fixtures. (Yippee!) I guess there's a first time for everything!

Day 201 - rain, rain, rain, rain!

Rain rain rain! Will it ever stop?
There were only 4 working days over the last 2 weeks because of the rain, and it rained yesterday and is raining now, and is forecast to rain the rest of the week! Arrgh!
This is the fourth week (yes!) of working on the trusses, and we are nowhere near being ready for shingling. Yes, four weeks is a very long time, and all of this rain is part of the reason!
Charles was meeting Dave White, who is doing the septic today. As we're getting on for winter, this needs to get done pronto otherwise freeze-up will be here and we will have a problem.
We have selected our garage door supplier. Mark wanted to get the elongated panels but they aren't available in the size of our doors, although the doors are available in taupe (Garaga calls it "claystone"). The garage door guy won't install the doors until the floors have been poured.
Sunday, October 23, 2005
Day 199 - a rainy Sunday...
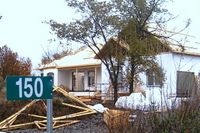
This photo shows a couple of things. First, sometime over the past few weeks, our municipal street number sign was installed. This is so the 911 emergency services (fire, ambulance, etc) can find your house. Secondly, the photo also shows that the garage windows were installed yesterday.
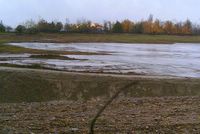
Looking forward... the forecast for the next week is: rain, except for Friday.
Saturday, October 22, 2005
Day 198 - more updates
Other updates from the meetings I posted about on Day 194:
- * We picked up the exterior locks from Preston Hardware. We actually only ended up having to buy one extra lock in order to do the split finish. So that was really good.
- * The California Closets lady came by on Tuesday and gave us a quote for the closets in the master bedroom. It was quite a bit higher than we had expected. Given the trend for some of the major expenses (i.e. over-budget), it seems unlikely that we will be able to get a fancy setup like that. Although California Closets started with a young guy and a truck in California, it is now a Canadian company. (surprise surprise!)
- * We didn't have a budget review as planned on Wednesday evening as Charles hadn't completed the expense computations, etc. I did a very rough calculation and guestimated that we have already used up our entire contingency allocation. We talked about the stone work. Conrad's labour estimate is 50% higher than our actual budgeted amount for the stonework, and that's without the material cost! So that quickly blew the lid off the contingency.
- * We have rebooked the fireplace appointment (I think the new appointment is next Wednesday).
- * Today our new snowblower was delivered. It's a Bolens, so that means it is green with a cream coloured auger. As far as I can tell, the colour is probably the only thing that distinguishes it from the other brands manufactured by MTD. The other MTD brands are Cub Cadet, Troy-bilt, Yard-Man, Yard Machines, Bolens, White Outdoor, McCulloch, and Cub Cadet Commercial. MTD doesn't make a snowblower in all of these brands.
When Charles was here on Wednesday, he gave us a list of homework:
- * Plumbing fixtures: as noted on Day 194, we have an appointment at Mondeau to review our fixture list before ordering. We wanted to do this anyway to make sure it is all correct, but the guy at Mondeau insisted on it. We will place the order on Monday.
- * Exterior door hardware: as noted above, we have picked this up. This means that the doors can be locked and the house can be secured once all the doors are installed.
- * Garage doors: we have narrowed the field down to two people, and have a couple more questions for one of the suppliers just to make sure we are comparing the same things.
- * Light fixtures: we have selected all of these products, and will order them in late November/early December.
- * Flooring: we have selected all the flooring, and will have a meeting with Mike Burley (of Burlco flooring) in a few weeks.
- * Cabinets: we have selected the cabinets. Once the interior partitions are in place (drywall doesn't have to be installed), Heinz will come out to the house and take accurate measurements so he can build the cabinets to the actual dimensions (which always differs from the planned dimensions).
- * Propane supplier: we need to find one!
- * Communications: need to call 310-Bell to get some cable delivered. Also need to get some coax to hook up the cable (although we may get a satellite dish).
So the only things we need to do (that we haven't done or are in progress) are select a propane supplier and get the communications cable.
We also need to do some research for a chain link fence installer, and Freda is thinking about the paint colours.
So many details.... we are sooo glad we made most of our selections a long time ago.
Friday, October 21, 2005
Day 197 - Start of roof sheathing

The roof framer and his crew, as well as Charles' crew are relaxing for a few minutes at the end of a long day. It was a beautiful day (no rain!) so more of the trusses were placed, and the plywood sheathing on the roof was started. So far, two lifts of plywood have been placed. Each lift is 60 sheets of 4'x8', or 32 square feet. That means 3,840 square feet of plywood have been installed, and it's not quite half done!



Thursday, October 20, 2005
Day 196 - truss progress

Fairly good progress today. The roof framer and his crew came today to help out with completing the truss installation and the roof sheathing. Unfortunately, a lumber yard was supposed to deliver three lifts of plywood for the roof but didn't because they "ran out". So the roof framer & crew did what they could and then left because the sheathing wasn't delivered.
What's a lift of plywood? 60 sheets, which covers 1,920 square feet 32 square feet at a time...
We had a meeting at 5:15pm with John Finlayson, of New Look Windows, to discuss the issues with the missing grills in the windows and the incorrect doors. John is undertaking to correct the issues with the missing grills and door glass.
When we were talking with John, Charles showed up with the first lift of plywood in the back of his truck. It must be very helpful to be unflappable like Charles when you're in construction, because something is bound to go wrong somewhere. Personally, I would have been very upset with someone who committed to deliver something that was needed for your critical path, and then didn't. If Charles was upset he sure didn't show it.
Tuesday, October 18, 2005
Day 194 - Updates
Freda has made lots of appointments for us this coming week...
- Tues Oct 18th - California Closets appointment
- Wed Oct 19th - Cost review with Charles, followed by budget and plan review
- Thur Oct 20th - Meeting with Charles and the window guy at the building site to review the numerous mistakes. (meeting not yet confirmed)
- Fri Oct 21st - Fireplace (meeting booked and then cancelled, trying to rebook)
- Sat Oct 22nd - Our new snowblower gets delivered
- Mon Oct 24th - Plumbing review and order @ Mondeau
So far, we have ordered the interior doors from Frank's. We have also reviewed the door hardware and are ready to order that from Preston Hardware.
It was another rainy day here in Ottawa and forecast for more of the same for most of this week. In order to make some real progress on the roof, Charles has arranged for a roof framer and a couple of his assistants to come on Wednesday and get the trusses properly in place and sheathed so the shinglers can take care of the roof. We need to get the roof on and windows/doors installed so we can make a bank draw.
Day 193 - Windy weekend
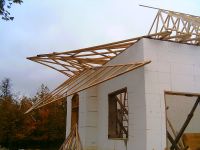
This happened because the trusses were just tacked into place when the crane was here (in order to make best use of the crane time - which is about $2,000 per day). I guess there wasn't quite enough bracing to hold it all up.
Sunday, October 16, 2005
You can't do that!!!

However, as a cost-saving measure (or should I say profit-creating (for them) and inconvenience-creating (for us) measure), Kwikset (a Black & Decker company) no longer offers this "split finish" option. And they don't even offer this lever in the Venetian Bronze finish.
Freda and I were quite disappointed about this, and thought we would have to choose a different lever to something that was available in both VB and SN. We went to Home Depot on Friday (to see if they had any split finish options), where I encountered a person who must have been the most bitter man in the entire world (who ranted about everything!), and said nobody did split finish, except Preston Hardware who could only do that on handlesets (like you see on front doors). FYI... Preston was where we originally found the door hardware that we liked.
We went down to Preston Hardware on Saturday and discussed this dilemma with Armand, who told us "the Pembroke lever was available in the now discontinued Oil Rubbed Bronze finish - which is very similar to Venetian Bronze except it does not have highlights like VB. And I have a few inactive levers in ORB downstairs. I could switch the lever and the rose on the exterior so you can have that split finish with ORB outside and SN inside, but it will cost about $20 more per handle."
We looked at the plan and thought we would only need three handles like that, so we said okay. When Armand was switching the handles, we realized that we actually do need some inactive handles for the closets anyway, so we can use the newly liberated SN levers with the inactive fastenings from the ORB boxes. This means that it doesn't cost us any more at all! Fabulous. (I will save my rant about Kwilkset/Black&Decker "cost savings" for some other time.)
The only drawback is that we will need to buy two locks in order to create the split finish for the locks, otherwise the lever and the lock will have a different finish when looking at it from the inside. That will cost us a little extra and unfortunately there are not really any other options for that.
This was yet another example how the Orange Borg is not necessarily the best option for finding supplies...
Friday, October 14, 2005
Day 189 - Trusses and windows

The crane arrived on Wednesday to lift the rest of the large trusses into place. There are just a few smaller trusses on the ground now, that will be placed once the all the large trusses are installed completely. These are the trusses over the garage.

I find it totally strange that someone at the window manufacturer didn't question this unusual configuration...
Tuesday, October 11, 2005
Door updates
However, as Bob at the Kanata HD was quite helpful, so we thought we would give them a chance at supplying our doors despite this annoyance. So we asked HD for a price, as well as the small local building supply store. Guess what? The small local place beats HD's price by about 15%, which gives them the advantage even if we order and get the 10% with the acquisition of a new HD credit card!
So the moral of the story is... don't assume the Orange Borg always has the best prices...
Meanwhile, back at the ranch...
The crew was putting up more trusses at the building site today. I dropped by to give Charles a cheque and gave them moral support for a short while. The crane wasn't available for a full day today, so he will be out there tomorrow (Wednesday). One full day of the crane should complete the crane work for installing the trusses.
And the windows and doors will probably be arriving on Friday, which means the 30 day clock will start ticking then.
Sunday, October 09, 2005
Decision revision...
On the plus side, this will save a little bit of $$ in the budget in case the french doors we would like to have are dear.
Saturday, October 08, 2005
Decisions and indecisions...
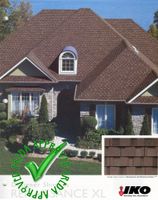
(click any picture for larger view)
First the decisions... The shingles are IKO Renaissance XL in Weathered Slate.
We still need to select the stucco colour and the soffit/fascia colour. All we can say right now is that the stucco will be a taupe or something like that, and the soffit/fascia will not be white.

(top left) Interior doors are Masonite Palazzo series, Bellagio model (two curved panels). We will use the 1 3/4" thick doors for the bedrooms and bathrooms to block more noise, and the 1 3/8" thick doors for the closets, etc, to save a little $$ on the budget. These doors are solid and will be faily heavy, so we will use the ball bearing hinges on these. We have decided to use the slightly taller 7' tall doors instead of the standard 6'8" doors, as the cost is quite minimal (only $10-15 per door).
(top right) This 9-light door is what we would like to have for the french doors at the foyer and the solarium. We haven't been able to get a price on these yet so are crossing our fingers that the price will permit it. The other option is just to use a 1-light door.
(bottom) This is the door hardware we selected from Kwikset. The exterior handleset is the Hawthorne in Venetian Bronze (pretty much the same as the Oil Rubbed Bronze finish that is on our exterior light fixtures). We will use the Pembroke lever in Satin Nickel on the interior doors. This hardware used to be known as Society Brass, but is now known as Kwikset UltraMax Signature, which is a Black & Decker company.
We had planned on using dummy levers on all the closets, but are going to switch to simple knobs on the smaller closet doors instead so we can stay within our budget.

We originally decided on the teak engineered flooring. However, after looking at it in various lighting conditions, Freda realized that it had a greenish tone and it wouldn't look too great with the cabinets in the kitchen. Good call! So we made another trek to Burlco Flooring in Merrickville and found this Asian Mahogany engineered product that we think looks pretty good with the cabinets.
Asian mahogany (Keruing) is harder but not as stable as teak, which we had originally selected, although it is harder and more stable than oak which is the most common hardwood flooring in North America. Asian Mahogany is 1520 on the Janka Hardness Scale, Red Oak is 1290, Maple is 1450, and Teak is 1155. [American] Cherry is also something we considered, althought it is softer (950 Janka) but just as stable as oak. The hardness of the wood is relevant as it indicates how easy (or hard) it will be to dent the wood surface - that's what the Janka Hardness test measures - the force required to embed a 0.444-inch steel ball to half its diameter into the wood and is one of the known ways to test the ability and wear of hardwood flooring. As you can understand from this, the higher the number, the harder the species of wood.
However, hardness isn't the only important factor to consider. Stability - the aptitude of a wood species to maintain a moisture level, thereby making it more or less prone to shrinkage and swelling - also important as it says how much the wood will moves as conditions change throughout the season with the varying humidity. With solid wood flooring, less stable woods cause the floor to squeak. The challenge for manufacturers of engineered flooring products is to create a base that is strong enough to withstand the movement of the finish veneer layer without cupping.
The colour of this photo may not be correct, as it depends on your monitor settings, but it looks pretty accurate on mine! :^)
Decisions still to come...
Garage doors...
Day 183 - more trusses

These are the cathedral trusses over the great room that were installed with the assistance of the crane on Thursday.

Charles says it is a complicated roof -- it sure is.

And yes, the amount of time it is taking to install the trusses is scaring us somewhat, as our current house is quite possibly sold with an end of January closing!
On the other hand, Steve Berry was able to find someone who wanted some of the rock fill that needed to dispose of, and hauled away about 15 loads or so on Friday. Fabulous!
Thursday, October 06, 2005
Day 182 - trusses

Oct 6/05: This is a closeup to show all the nails here - the three trusses are fasted by 5 nails every 4 inches (from each side). The joist hanger has 25 nails on each side, for a total that is, um, a lot of nails.

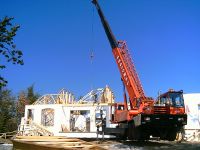


Wednesday, October 05, 2005
Another record high day for Ottawa

Compare today's weather for Winterpeg (haha) and Ottawa - where would you rather be? No question in my mind....
The crew was making the final preparations today for the arrival of the crane (scheduled for tomorrow) to lift the trusses into place. Yesterday, the forecast for Thursday was for rain (which would not have been good) but the current forecast is now the same as today (mainly sunny) with a high of 24C, with the rain shifted out to Friday.
Tuesday, October 04, 2005
Day 180 - dead level

Day 180 - Charles went around the building with me today showing me how plumb the walls are. This was with 6 foot level, and not one of those kind where the bubble is fixed. :^)))


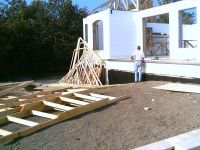

Sunday, October 02, 2005
Day 178 - Trusses, trusses, and more trusses.

(click any picture for larger view)
A third load of trusses was delivered on Thursday - that's these massive ones shown on the the left. The trusses enable all of the interior walls to be free standing (not load-bearing).
This is pretty amazing when you think about it. I guess it can be done because there is no floor (with the loading that presents) above.

These trusses are tied together with 2x4s (can't really see them in this picture). One of the major causes of roof failure in a hurricane is the failure of the truss structure generally because the trusses are often fastened together only by the plywood sheathing.
I mentioned hurricanes and hurricane clips in an earlier posting. Roofs that are blown off in a hurricane usually fail because the roof itself generates a low-pressure area (due to the Bernouilli effect - the roof acts like an airfoil which makes sense if you think about). This low-pressure zone vaccuums the shingles and plywood sheathing off the roof. Since the trusses in a mass-production houses are rarely fastened together by anything except plywood, a single failure generally causes a cascading failure. You can read more about it in this Nov/96 paper by "Hurricane Damage to Residential Structures: Risk and Mitigation" by Jon K. Ayscue, Johns Hopkins University, Baltimore, Maryland.
